Newsletter
Transitioning from ISO 9001:2008 to ISO 9001:2015
What is new with ISO 9001:2015? At Z-AXIS we found that—between our existing quality management system and the way we use our our strategic plan to guide our daily operations—were already meeting most of the new requirements. We just had to formalize and document things we are already doing. There were minimal system changes, and in many ways the new standard is even easier for us to meet than the old one.
The biggest impact for us is that the new standard puts less emphasis on documenting procedures, and more emphasis on understanding “cause and effect” and on managing risks to quality.
Managing risk
We’ve always had a pre-production (or new product introduction) meetings. In these meetings our manufacturing engineers, electrical engineers, production managers, purchasing team, quality and customer service staff work together to review how we’re going to manufacture a product. We naturally look for potential problem areas and how to avoid them as part of this.
Now risk management is a formal and documented step in the meeting. It turns out that this really does help us do a more thorough analysis. We document each risk, assess its impact on our workers as well as our customers, define the steps we will take to manage it, and assign who is responsible for each step. The document remains open until we prove that the actions have been completed and that that they were effective.
For example, a new assembly we’re making has magnets in it. We had planned to place the magnets in a tray for assembly workers to pick from. The pre-production meeting team identified a risk that the magnets could shift and stick together if the tray was jarred. This would make it difficult to pick them from the tray, making the production team’s work harder and potentially delaying production for the customer. To reduce this risk, we will create work- in-process trays with an individual cell for each magnet. We documented who is accountable for implementing that and when.
We have added a formal risk assessment step into other processes throughout the company; for example our engineering change notice (ECN) process in the engineering department.
Involving top management
ISO 9001:2015 includes rule changes that are designed to increase top management involvement in quality, rather than leaving responsibility for quality to a “management representative” (e.g. quality manager). There is no change here for us, since our management team has always been actively involved in our strategic plan, key performance indicators (KPIs) and monthly reviews. This is because we not only have a strategic plan, but actually use it to guide daily activities.
The strategic plan details specific actions that we will take each quarter. It has KPIs we track to measure our progress. Our entire management team participates in monthly reviews and shares responsibility for meeting the goals.
Using customer feedback
We have always prioritized regular contact with customers by phone or face-to-face. We typically act on customer feedback as soon as it comes in. If there is a problem, we jump on it. If it’s praise for a job well done, we usually remember to share it with the team… but this doesn’t always happen on busy days. And all days are busy.
ISO 9001:2015 increases the requirement to document and use customer feedback. So one change we made is to log customer feedback into a database. We still take immediate action on problems, but now we also review the collected feedback in the monthly management meeting.
This gives us a bigger-picture view of the customer feedback and lets us identify systemic changes or actions we can to take to meet our KPIs. In addition, the positive feedback now gets its fair share of attention and we use it to reinforce what’s working.
More interested parties
Finally, ISO 9001:2015 encourages companies to consider the impact of actions on all “interested parties,” such as internal employees, as well as customers.
ISO, we were years ahead of you on this.
Our core strategic goal has long been: happy employees and happy customers. That’s it. We believe that happy employees lead to happy customers and that leads to profit, earnings and growth. People laugh at this as an overly-simple philosophy, but it is really true. Good people like to make good products they can be proud of. So we are already considering and measuring the impact of everything we do on our employees’ ability to do good work. No change for us there.
Quality manual: yes or no?
ISO 9001:2008 required companies to create a quality manual and document their processes. ISO 9001:2015 requires more proof that you actually use your quality processes and that they are effective. While it has expanded what you must document, it has become less specific on how you must document it.
Some companies think this means they can throw out their quality manual, but a good quality manual is still a good format for consolidating all the required documentation under the new standard. On the other hand, companies who achieved certification by having a wonderful quality manual but are not using it probably don’t have the necessary systems in place to meet the new standard.
The process of updating to ISO 9001:2015 was time-consuming but has given us a fresh perspective on our quality management system, reinforced what we were doing right, and given us additional tools to do better.
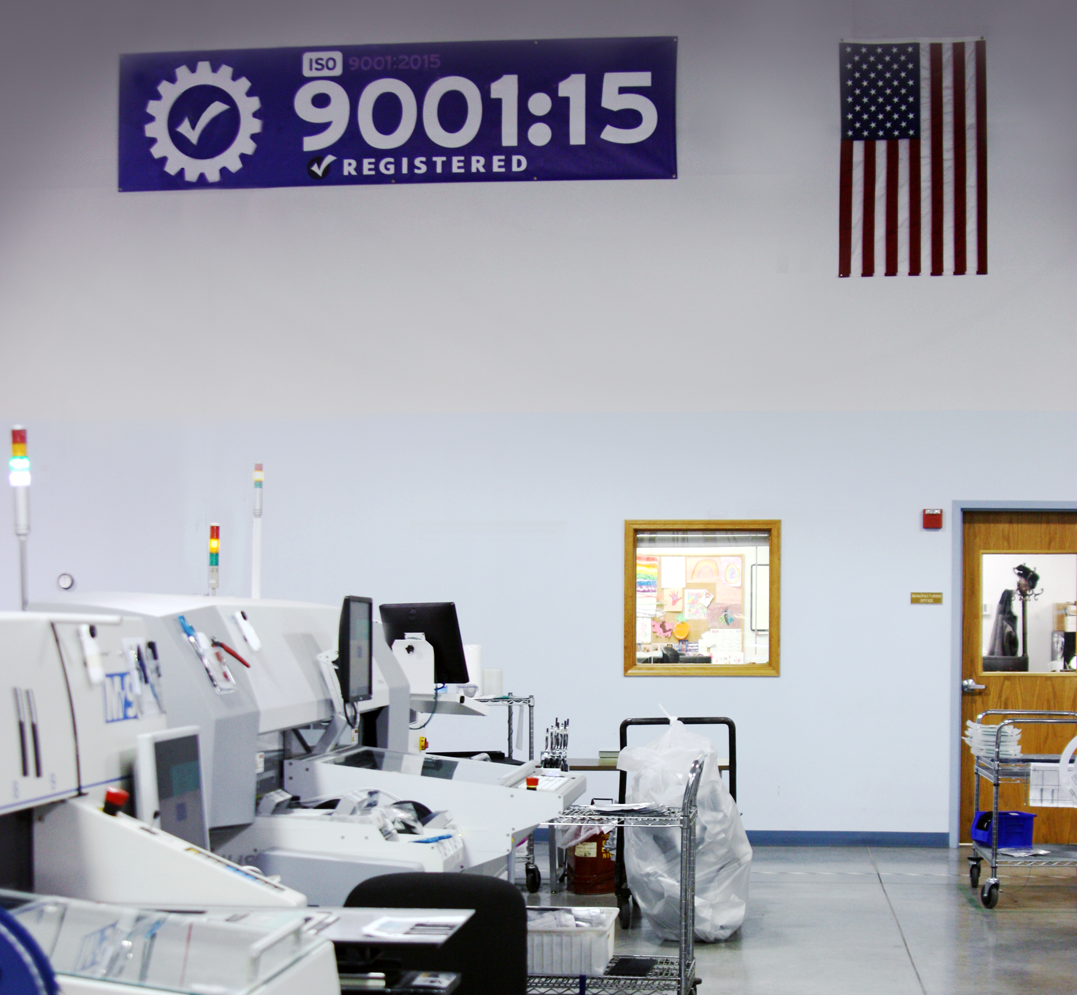
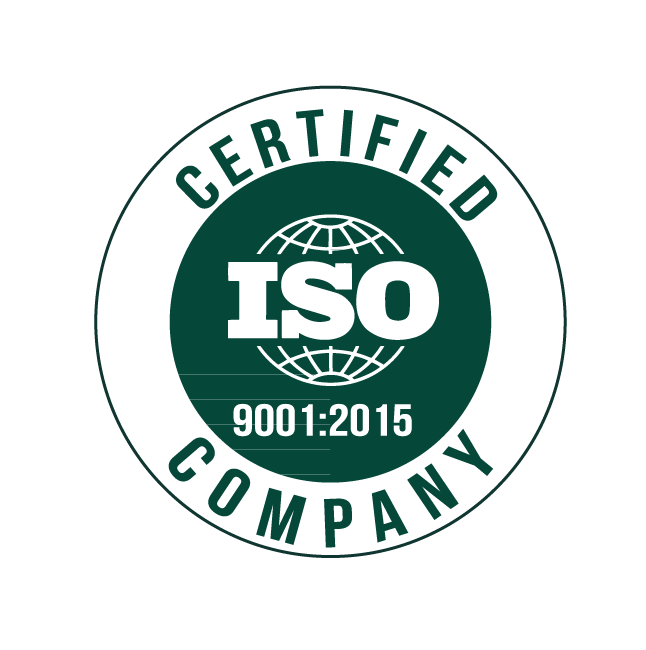